Worker Industrial
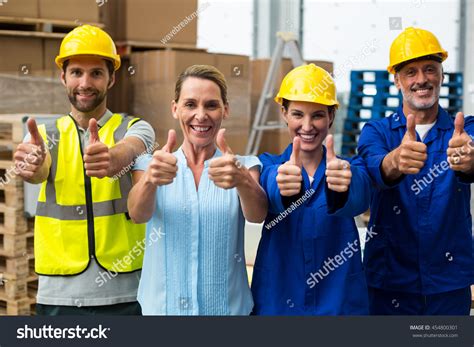
In today's rapidly evolving industrial landscape, the importance of skilled workers cannot be overstated. The world of industrial operations is dynamic and complex, requiring a highly specialized workforce to ensure efficient and safe functioning. This article delves into the critical role of industrial workers, exploring their diverse responsibilities, the challenges they face, and the strategies employed to overcome them. By examining real-world examples and industry insights, we aim to provide a comprehensive understanding of this vital workforce.
The Evolution of Industrial Work
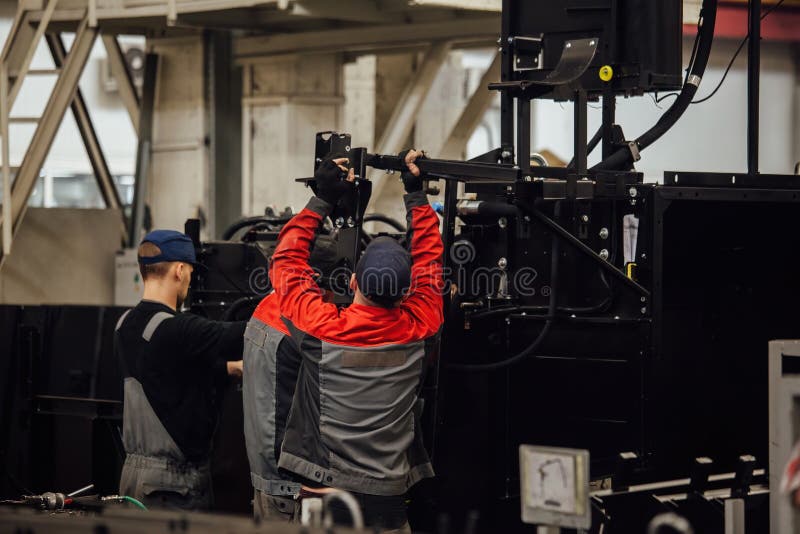
Industrial work has undergone a remarkable transformation over the past century. What began as manual labor in factories and mills has evolved into a highly sophisticated and technologically advanced field. The introduction of automation, robotics, and digital technologies has revolutionized industrial processes, enhancing productivity and efficiency. However, this evolution has also brought about new complexities and demands on the workforce.
The modern industrial worker is now expected to possess a unique blend of technical skills, problem-solving abilities, and adaptability. They must navigate complex machinery, interpret data, and make quick decisions to optimize production and maintain safety standards. As industries continue to innovate and adapt, so too must the skills and knowledge of the industrial workforce.
Key Responsibilities of Industrial Workers
Industrial workers are the backbone of any manufacturing or production facility. Their role is multifaceted, encompassing a wide range of critical tasks. Here are some of the key responsibilities that define the industrial worker’s role:
- Operation and Maintenance of Machinery: Industrial workers are responsible for operating and maintaining the complex machinery that forms the backbone of industrial processes. This includes understanding the technical specifications of various machines, troubleshooting common issues, and ensuring timely maintenance to prevent breakdowns.
- Quality Control and Assurance: Ensuring product quality is a vital aspect of industrial work. Workers must meticulously inspect and test products to meet industry standards and client expectations. This involves utilizing specialized tools and techniques to identify and rectify defects, ensuring that only the highest-quality products reach the market.
- Health and Safety Compliance: The well-being of industrial workers and their colleagues is a top priority. Workers must adhere to strict health and safety regulations, wearing appropriate personal protective equipment (PPE) and following safety protocols to prevent accidents and injuries. They also play a crucial role in identifying potential hazards and implementing safety measures.
- Data Analysis and Process Optimization: With the integration of digital technologies, industrial workers now handle vast amounts of data. They must be adept at interpreting data to identify inefficiencies and bottlenecks in production processes. By analyzing trends and patterns, workers can suggest improvements to enhance productivity and reduce costs.
- Collaboration and Communication: Industrial work often involves cross-functional collaboration. Workers must effectively communicate with colleagues from various departments, including engineering, maintenance, and management. Clear and concise communication ensures that everyone is aligned and working towards common goals.
Challenges and Strategies
Despite the crucial role they play, industrial workers face numerous challenges in their day-to-day operations. These challenges can impact productivity, safety, and overall job satisfaction. Here are some of the key challenges and the strategies employed to overcome them:
Skill Gap and Training
As industrial processes become more complex, the skill requirements for workers increase. Many industries struggle with a skills gap, where the demand for skilled workers exceeds the available talent pool. To address this, companies are investing in comprehensive training programs. These programs not only focus on technical skills but also emphasize soft skills such as communication, problem-solving, and adaptability.
Workplace Safety and Well-being
Ensuring the safety and well-being of industrial workers is paramount. However, the nature of industrial work often involves potential hazards and risks. To mitigate these risks, companies are implementing rigorous safety protocols and providing extensive safety training. Additionally, initiatives to improve workplace ergonomics and mental health support are gaining traction, recognizing the importance of worker well-being for overall productivity.
Technological Integration
The integration of advanced technologies like robotics and artificial intelligence (AI) in industrial processes presents both opportunities and challenges. While these technologies can enhance efficiency, they also require workers to adapt and acquire new skills. Companies are adopting a hybrid approach, combining human expertise with technological advancements. This ensures that workers remain at the forefront of decision-making, utilizing technology as a tool to enhance their capabilities rather than replace them.
Data-Driven Decision Making
With the abundance of data available in industrial settings, making sense of this data and using it effectively is crucial. Companies are investing in data analytics tools and training workers to interpret and utilize data. By leveraging data-driven insights, industrial workers can make informed decisions, optimize processes, and drive continuous improvement.
Performance Analysis and Metrics
Measuring the performance and impact of industrial workers is essential for continuous improvement. Companies utilize a range of metrics and analytical tools to assess worker productivity, efficiency, and safety performance. These metrics help identify areas for improvement and guide training and development initiatives.
Performance Metric | Description |
---|---|
Productivity Index | Measures the efficiency of workers in producing goods or delivering services. It takes into account factors such as output volume, quality, and resource utilization. |
Safety Incident Rate | Tracks the frequency of safety incidents or accidents in the workplace. It helps identify areas where safety protocols need to be reinforced or improved. |
Quality Assurance Score | Evaluates the effectiveness of workers in ensuring product quality. It considers factors like defect rates, customer feedback, and compliance with industry standards. |
Training Completion Rate | Monitors the participation and completion of training programs by workers. It indicates the level of skill development and the company's commitment to continuous learning. |
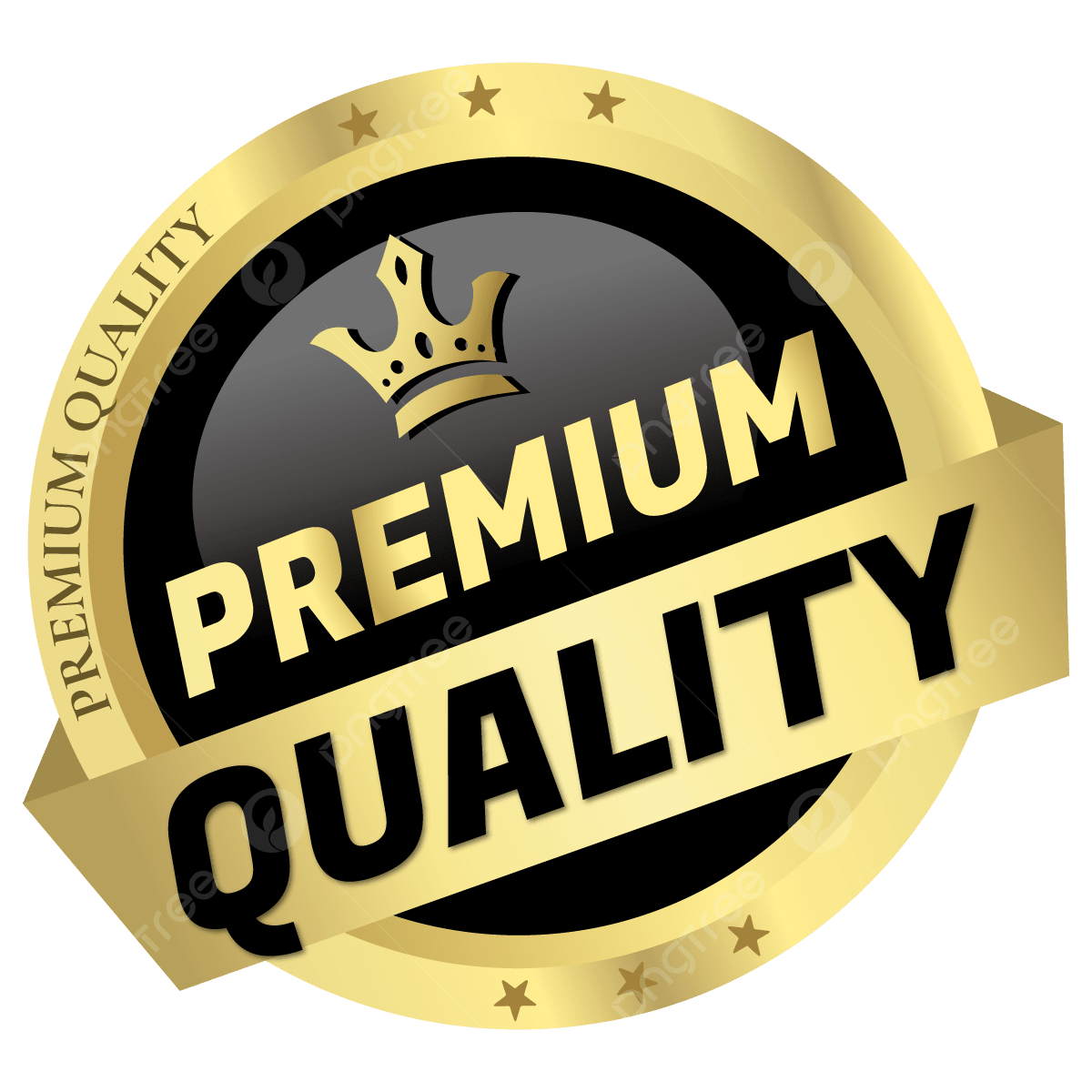
Future Implications and Opportunities

As we look towards the future, the role of industrial workers is poised for significant evolution. The continued integration of advanced technologies and the rise of Industry 4.0 will bring about new challenges and opportunities. Here are some of the key future implications and potential avenues for growth:
The Rise of Smart Factories
The concept of smart factories, where digital technologies and automation are seamlessly integrated, is gaining momentum. These factories will require a new breed of industrial workers who are skilled in operating and maintaining advanced machinery, analyzing data in real-time, and making data-driven decisions. Workers will need to embrace a continuous learning mindset to keep up with the rapid pace of technological advancements.
Upskilling and Reskilling Programs
To stay competitive in the evolving industrial landscape, companies will need to invest heavily in upskilling and reskilling programs. These programs will focus on helping workers adapt to new technologies and processes, ensuring they remain relevant and valuable assets to the organization. Continuous training and development will become a key differentiator for industrial workers, setting them apart in a highly competitive job market.
Collaboration with AI and Robotics
The future of industrial work will see increased collaboration between humans and machines. AI and robotics will handle repetitive and physically demanding tasks, while workers will focus on more complex and creative aspects of the job. This collaborative approach will enhance productivity and safety, allowing workers to leverage their unique skills and expertise alongside advanced technologies.
Sustainable and Eco-Friendly Practices
With growing environmental concerns, the industrial sector is under pressure to adopt more sustainable practices. Industrial workers will play a crucial role in implementing and adhering to eco-friendly processes. This may involve adopting new technologies, optimizing energy usage, and reducing waste. By embracing sustainability, workers can contribute to a greener and more responsible industrial future.
Remote and Hybrid Work Models
The COVID-19 pandemic has accelerated the adoption of remote and hybrid work models in various industries, and the industrial sector is no exception. While certain aspects of industrial work require physical presence, remote monitoring, data analysis, and decision-making can be effectively done remotely. This shift towards remote work will offer industrial workers greater flexibility and work-life balance.
Conclusion
Industrial workers are the unsung heroes of the industrial landscape, driving innovation, efficiency, and safety. Their diverse skill set, adaptability, and commitment to continuous learning make them invaluable assets to any industrial organization. As industries continue to evolve, the role of industrial workers will become even more critical. By investing in their skills, well-being, and future-ready capabilities, companies can unlock the full potential of this vital workforce, shaping a brighter and more sustainable industrial future.
What are some common challenges faced by industrial workers?
+Industrial workers often face challenges such as physical demands, repetitive tasks, and exposure to potential hazards. Additionally, keeping up with technological advancements and adapting to changing processes can be demanding.
How do companies address the skills gap in the industrial sector?
+Companies tackle the skills gap by investing in comprehensive training programs that focus on both technical and soft skills. They also collaborate with educational institutions to develop industry-specific curricula and provide apprenticeship opportunities.
What role does technology play in the future of industrial work?
+Technology will play a pivotal role in the future of industrial work, with the rise of smart factories and Industry 4.0. Industrial workers will need to collaborate with advanced technologies, leveraging their expertise alongside automation and AI to drive innovation and efficiency.